Siempre he creído que el mantenimiento es mucho más que un simple 'parcheo' cuando algo se rompe. Es una disciplina de ingeniería estratégica, el motor silencioso que impulsa la rentabilidad y la seguridad en cualquier operación industrial. En este artículo, comparto contigo mi visión sobre cómo hemos pasado de arreglar lo averiado a anticipar el futuro de las máquinas. Exploraremos los pilares de la ingeniería en mantenimiento, desde el perfil del profesional que hace magia detrás de escena, hasta las diferentes estrategias que hoy son clave: correctivo, preventivo, predictivo y proactivo. Y lo más emocionante, nos adentraremos en la revolución digital de la Industria 4.0, viendo cómo tecnologías como el IoT, la Inteligencia Artificial y los gemelos digitales están reescribiendo las reglas del juego. Prepárate para descubrir cómo el 'ingeniero de mantenimiento' de hoy no solo repara, sino que diseña el futuro de la planta.

Mantenimiento Industrial: De Apretar Tornillos a Diseñar el Futuro de las Plantas
Durante años, cuando alguien me preguntaba a qué me dedicaba, y les decía 'ingeniería en mantenimiento', a menudo veía una ceja levantada, como si pensaran en alguien solo apretando tornillos. ¡Qué equivocados estaban! El concepto de mantenimiento ha dado un giro de 180 grados. Aquello que antes se veía como un gasto inevitable, un ‘mal necesario’ que surgía solo cuando algo fallaba, hoy es una pieza central en la estrategia de cualquier empresa que aspire a ser competitiva, segura y sostenible.
Hoy, hablar de mantenimiento ya no es sinónimo de una simple reparación; es hablar de fiabilidad, de tener equipos siempre disponibles, de optimización de recursos y, en última instancia, de maximizar la rentabilidad. Y justo aquí es donde la ingeniería en mantenimiento industrial emerge como el verdadero pilar. Es la columna vertebral que soporta la productividad y eficiencia de cada máquina, cada sistema en una organización. Créeme, va mucho más allá de arreglar una avería; es un campo integral que aplica principios de ingeniería robustos, las mejores prácticas de gestión y herramientas tecnológicas de vanguardia para asegurar la máxima vida útil de la maquinaria, minimizar esas paradas inesperadas que tanto duelen al bolsillo y garantizar que todo opere con la máxima eficiencia y seguridad.
Tabla de Contenido
- El Rol Estratégico del Ingeniero de Mantenimiento
- Diferenciando Conceptos Clave: Un Universo de Especialización
La ingeniería de mantenimiento es, en esencia, la formalización técnica y estratégica de todas las actividades dedicadas al cuidado de los activos. Mientras que un técnico se concentra en ejecutar una tarea específica, un ingeniero piensa en el 'porqué', el 'cuándo' y el 'cómo' de esa tarea, en el contexto de un plan maestro. Su misión principal es diseñar e implementar estrategias que garanticen que los equipos estén siempre listos para funcionar, y que lo hagan al menor costo posible. Esto requiere un conocimiento profundo que no se limita a lo mecánico o eléctrico; abarca análisis de datos, gestión de proyectos, planificación de recursos y la crucial habilidad para analizar la causa raíz de los fallos. Un profesional en esta área, al que cariñosamente llamamos un ing en mantenimiento industrial, es por naturaleza un solucionador de problemas, un estratega que mide el éxito en términos de optimización del ciclo de vida del activo (LCCA) y retorno de la inversión (ROI).
El Rol Estratégico del Ingeniero de Mantenimiento: Más que un Héroe Ocasional
Para mí, el ingeniero de mantenimiento es una figura clave, casi un 'médico de la planta'. Sus responsabilidades son amplias y absolutamente críticas para el éxito operativo. Permíteme contarte algunas de sus funciones principales:
- Análisis y Diagnóstico: Utiliza herramientas y técnicas avanzadas para evaluar la condición de los equipos, predecir posibles modos de fallo y diagnosticar problemas recurrentes. Aquí es donde una sólida base en ingeniería mecánica en mantenimiento industrial se vuelve indispensable, combinada con conocimientos de electrónica y control.
- Planificación y Programación: Diseña los planes maestros de mantenimiento, definiendo las frecuencias, los procedimientos y los recursos necesarios para cada intervención, ya sea preventiva o predictiva. Esto es como armar un rompecabezas gigante, donde cada pieza debe encajar a la perfección.
- Gestión de Recursos: Administra el presupuesto del departamento, gestiona el inventario de repuestos críticos y coordina al equipo técnico. Se asegura de que todos cuenten con la formación y las herramientas adecuadas; al final, su gente es su mayor activo.
- Implementación de Mejoras: No se conforma con el statu quo. El ingeniero en mantenimiento está siempre buscando oportunidades para mejorar: modificando un componente para que dure más, optimizando un plan de lubricación o implementando una nueva tecnología de monitoreo. Es el motor de la mejora continua.
- Garantía de Seguridad y Cumplimiento Normativo: Se asegura de que todas las actividades de mantenimiento se realicen bajo estrictas normas de seguridad (como los estándares OSHA) y cumpliendo con las regulaciones ambientales y de calidad. La seguridad del personal y la operación siempre es lo primero.
La gran diferencia entre la gestión de mantenimiento tradicional y la que propone la ingeniería en mantenimiento radica en el enfoque proactivo. En lugar de esperar a que ocurra una falla para reaccionar (el temido mantenimiento correctivo), se busca anticipar y prevenir los fallos (mantenimiento preventivo) o, idealmente, predecir con exactitud cuándo es el momento preciso para intervenir (mantenimiento predictivo). Esta visión estratégica transforma radicalmente el departamento de mantenimiento: de ser un simple centro de costos, pasa a ser un verdadero generador de valor, impactando directamente en la rentabilidad de la compañía. Es un cambio de mentalidad que he visto evolucionar a lo largo de mi carrera y que marca una diferencia abismal.
Diferenciando Conceptos Clave: Un Universo de Especialización
Dentro de este fascinante campo, es común escuchar varios términos que, aunque relacionados, tienen matices importantes. Entenderlos es crucial para comprender la amplitud de nuestra disciplina:
- Ingeniería en mantenimiento industrial: Este es el término paraguas, el más amplio. Se refiere a la disciplina general de aplicar principios de ingeniería para la gestión del mantenimiento en un entorno industrial. Lo abarca todo.
- Ingeniería de mantenimiento: A menudo se usa de forma intercambiable con el anterior, pero a veces puede tener una connotación más enfocada en la gestión, la estrategia y la confiabilidad (Reliability Engineering) que en los aspectos puramente técnicos de la ejecución. Es un término que enfatiza la parte estratégica.
- Ingeniería mecánica en mantenimiento industrial: Esta es una especialización. Se centra en la aplicación de los principios de la ingeniería mecánica (termodinámica, mecánica de fluidos, diseño de elementos de máquinas, etc.) específicamente al mantenimiento de equipos industriales. Si hablamos de rodamientos, bombas o transmisiones, este profesional es el experto.
- Ingeniería en mantenimiento: Un término más genérico que puede aplicarse a otros sectores fuera del industrial, como edificios (facility management), flotas de vehículos o infraestructura.
- Ing en mantenimiento industrial: Es la abreviatura coloquial y comúnmente utilizada para referirse al profesional que ejerce la ingeniería en mantenimiento industrial. Es nuestro apodo en la industria.
Todas estas áreas, aunque distintas, convergen en un objetivo común: la salud de los activos. Un plan de estudios moderno en ingeniería en mantenimiento industrial integra conocimientos de todas estas ramas. Incluye desde termodinámica y mecánica de materiales hasta estadística, gestión de proyectos, sistemas de información (CMMS), y ahora, cada vez más, ciencia de datos e inteligencia artificial. La formación es interdisciplinaria porque los desafíos lo son. Piensa en esto: un fallo en un motor puede tener una causa raíz mecánica, pero su detección temprana puede depender de un sensor electrónico, y su gestión eficiente, de un software de mantenimiento. El profesional de la ingeniería de mantenimiento debe ser capaz de orquestar todos estos elementos para lograr una sinfonía de confiabilidad y eficiencia operativa, siendo el motor silencioso que impulsa la productividad industrial hacia adelante. Es una carrera que no solo ofrece un vasto campo laboral en sectores como la minería, manufactura, energía y aeronáutica, sino que también está en constante crecimiento y evolución, demandando profesionales altamente cualificados y con una mente abierta al cambio.
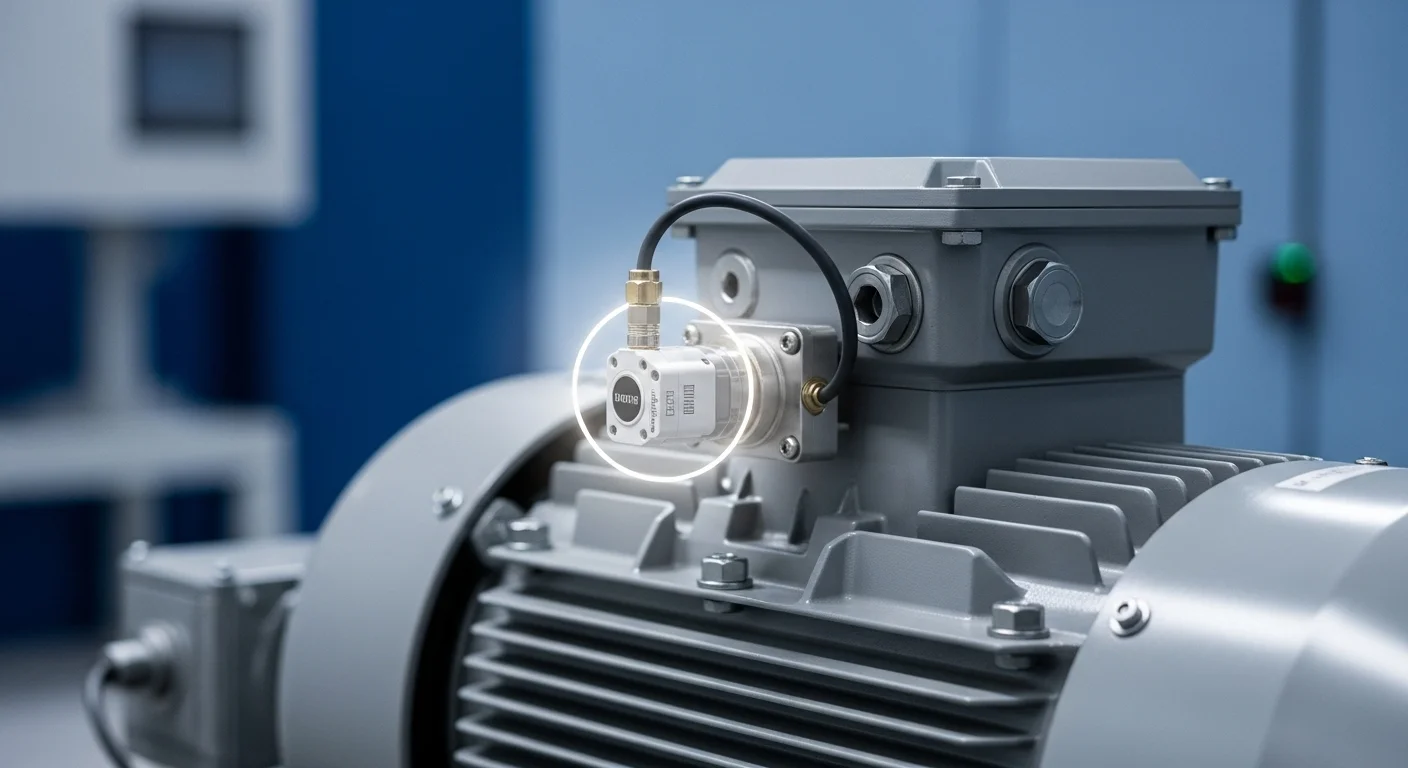
Estrategias Maestras: El Arsenal del Ingeniero de Mantenimiento Moderno
La clave de la ingeniería de mantenimiento es saber qué estrategia aplicar y cuándo. No hay una fórmula mágica que sirva para todo; la elección depende de muchísimos factores: cuán crítico es el equipo, qué tipo de fallos suele tener, cuánto nos costaría si dejara de funcionar, y la tecnología que tengamos disponible. Un buen ing en mantenimiento industrial es como un director de orquesta, desplegando un arsenal de metodologías para que cada máquina suene afinada. Estas estrategias se mueven en un espectro que va desde el enfoque más reactivo hasta el más proactivo.
1. Mantenimiento Correctivo: El 'Apaga Incendios' de la Fábrica
Esta es, sin duda, la forma más antigua y sencilla de mantenimiento. Básicamente, esperas a que el equipo falle para repararlo. Y sí, aunque a menudo se le critica, tiene su lugar. Yo lo divido en dos tipos:
- Correctivo no planificado: Imagina una emergencia. El equipo se rompe de repente y detiene la producción. Es la modalidad más cara, no solo por el tiempo que la planta está parada, sino por los posibles daños adicionales, las horas extras para el personal y el estrés que genera.
- Correctivo planificado: Aquí ya hay un poco más de cabeza. Detectas una pequeña anomalía (quizás un ruido raro, una pequeña fuga) que aún no ha causado un fallo total, y planificas la reparación para un momento oportuno, como una parada programada, minimizando el impacto.
Ventajas: La inversión inicial es mínima, y no hay que planificar mucho. Si no falla, no se gasta.
Desventajas: Los costos a largo plazo son altísimos, la imprevisibilidad es constante, y hay riesgos de seguridad. Depender solo de esto para equipos críticos es, simplemente, insostenible. La ingeniería en mantenimiento industrial busca reducir al máximo esta dependencia, reservándola solo para equipos de muy baja criticidad, cuyo fallo no afecte gravemente la operación.
2. Mantenimiento Preventivo: Adelantándose al Problema
Esta estrategia es el primer paso firme hacia la proactividad. El mantenimiento preventivo se basa en realizar intervenciones a intervalos predefinidos, ya sea por tiempo (cada seis meses), por horas de operación (cada 5000 horas) o por unidades producidas. El objetivo es simple: reducir la probabilidad de fallo al reacondicionar o reemplazar componentes antes de que lleguen al final de su vida útil esperada. Aquí, la visión de un profesional con formación en ingeniería mecánica en mantenimiento industrial es crucial para determinar la vida útil teórica de los componentes y definir tareas clave como lubricación, calibración o sustitución de piezas de desgaste.
Ventajas: Aumenta la fiabilidad y la disponibilidad de los equipos, permite una mejor planificación de paradas y recursos, y da un mayor control sobre el presupuesto de mantenimiento.
Desventajas: Existe el riesgo de 'sobre-mantenimiento', es decir, cambiar piezas que aún están en buen estado, lo que genera costos innecesarios. Además, no previene todos los fallos, ya que muchos no están directamente relacionados con la antigüedad del componente.
3. Mantenimiento Predictivo (PdM): Escuchando el Latido de las Máquinas
Aquí es donde la ingeniería de mantenimiento da un salto cuántico. Pasamos de prevenir por tiempo a prevenir por condición. El mantenimiento predictivo usa tecnologías de monitoreo para 'escuchar' el estado real del equipo en funcionamiento y predecir cuándo es probable que ocurra un fallo. Solo intervenimos cuando los datos nos lo gritan. Algunas de las técnicas que más utilizo son:
- Análisis de Vibraciones: Una de mis favoritas. Nos permite detectar desequilibrios, desalineaciones, holguras y problemas en los rodamientos de equipos rotativos. Es como el 'electrocardiograma' de la máquina.
- Termografía Infrarroja: Revela puntos calientes en sistemas eléctricos (malos contactos, sobrecargas) o mecánicos (problemas de fricción). Lo que el ojo no ve, la cámara lo muestra.
- Análisis de Aceite: Evalúa la salud del lubricante y nos dice si hay partículas de desgaste, indicando un deterioro interno del componente. Es como un análisis de sangre para la máquina.
- Ensayos no destructivos (Ultrasonido, Tintas Penetrantes): Detectan fisuras y defectos en materiales sin dañar el componente. Nos permite ver lo que hay debajo de la superficie.
Ventajas: Maximiza la vida útil de los componentes, reduce drásticamente las paradas no planificadas, minimiza el tiempo de intervención (porque sabemos exactamente qué reparar) y optimiza costos al evitar intervenciones innecesarias. He visto empresas reducir hasta un 70% sus fallos no planificados gracias a esto.
Desventajas: Requiere una inversión inicial en tecnología y en formación especializada para el personal. Pero, créanme, la inversión se recupera con creces.
Liderar la implementación de un programa de mantenimiento predictivo es una de las tareas más gratificantes y valiosas que un ingeniero en mantenimiento puede llevar a cabo. Es pasar de reaccionar a anticipar.
4. Mantenimiento Proactivo: Atacando la Raíz del Problema
Si el mantenimiento predictivo busca predecir el 'cuándo', el mantenimiento proactivo se obsesiona con eliminar el 'porqué'. Esta es la cúspide de la ingeniería en mantenimiento industrial. En lugar de solo anticipar y reparar fallos, investigamos la causa raíz (Root Cause Failure Analysis - RCFA) y aplicamos cambios para que el problema ¡simplemente no vuelva a ocurrir! Las acciones proactivas pueden ser:
- Rediseñar un componente para que sea más robusto y no falle.
- Mejorar los procedimientos de operación o limpieza.
- Cambiar las especificaciones del lubricante.
- Implementar un programa de alineación y balanceo de precisión.
Esta estrategia exige un conocimiento técnico profundo, muchas veces aportado por la ingeniería mecánica en mantenimiento industrial, y una mentalidad de mejora continua. No nos conformamos con arreglar; buscamos erradicar. Al hacerlo, extendemos la vida útil de los activos de forma exponencial y alcanzamos los niveles más altos de fiabilidad. Esta es la verdadera esencia de la ingeniería aplicada al mantenimiento: resolver problemas de forma permanente.
Metodologías Integrales: RCM y TPM
Además de estas estrategias, existen filosofías de gestión que las engloban y que han transformado la forma en que vemos el mantenimiento. Dos de las más importantes son:
- Mantenimiento Centrado en la Confiabilidad (RCM): Es un proceso estructurado que nos ayuda a decidir qué se debe hacer para asegurar que un activo físico siga cumpliendo su función en su contexto operativo. El RCM analiza los modos de fallo de cada equipo y define la estrategia de mantenimiento más apropiada (predictiva, preventiva, correctiva o incluso un rediseño) para cada tipo de fallo. Es un enfoque altamente analítico y riguroso.
- Mantenimiento Productivo Total (TPM): Esta es una filosofía que involucra a todos en la organización, desde la gerencia hasta los operadores de línea. Promueve el 'mantenimiento autónomo', donde los propios operadores realizan tareas básicas de mantenimiento y limpieza en sus equipos. Esto libera al personal especializado de ing en mantenimiento industrial para que se concentren en tareas más complejas, como el análisis predictivo y las mejoras proactivas.
La excelencia en la ingeniería de mantenimiento no es usar una sola estrategia, sino orquestar un 'cóctel' adaptado a la realidad de cada planta. Es la visión de ingenieros que entienden tanto la tecnología de los activos como la estrategia del negocio, logrando un programa de mantenimiento de clase mundial.

La Revolución 4.0: Forjando el Futuro de la Ingeniería de Mantenimiento
Cuando miro hacia atrás, veo cómo el mantenimiento ha evolucionado. Pero lo que está ocurriendo ahora con la Cuarta Revolución Industrial, o Industria 4.0, es algo sin precedentes. Su impacto en nuestro campo es simplemente transformador. La digitalización está convirtiendo las fábricas que antes conocíamos en ecosistemas inteligentes y totalmente conectados, y la ingeniería en mantenimiento industrial está en el epicentro de este cambio. Las tecnologías emergentes no son solo herramientas nuevas; están redefiniendo por completo nuestras estrategias y el rol mismo del ingeniero en mantenimiento. La capacidad de capturar, procesar y analizar volúmenes gigantescos de datos en tiempo real está elevando el mantenimiento predictivo y proactivo a niveles de precisión y eficiencia que antes solo soñábamos.
Tecnologías Habilitadoras de la Industria 4.0 en el Mantenimiento: Mis Aliados del Mañana
El futuro del mantenimiento, que para muchas industrias líderes ya es una realidad, se asienta sobre una serie de pilares tecnológicos que se han convertido en mis grandes aliados:
- Internet de las Cosas Industrial (IIoT): Para mí, es la base de todo. Imagina una red de sensores de bajo costo, discretamente instalados en cada equipo, midiendo en tiempo real variables críticas como vibración, temperatura, presión o consumo de energía. Estos sensores se comunican constantemente, enviando un flujo ininterrumpido de datos sobre la 'salud' del activo. El IIoT es lo que permite una monitorización continua y remota, dejando atrás las tediosas inspecciones manuales periódicas.
- Big Data y Análisis Avanzado: Si el IIoT genera una cantidad masiva de datos (el famoso Big Data), la verdadera magia ocurre cuando la ingeniería de mantenimiento aplica técnicas de análisis avanzado para convertir esos datos brutos en información útil y accionable. Podemos identificar patrones sutiles y correlaciones que un ojo humano jamás detectaría, permitiéndonos detectar anomalías en sus etapas más incipientes.
- Inteligencia Artificial (IA) y Machine Learning (ML): Este es el cerebro de la operación. Los algoritmos de Machine Learning pueden 'aprender' del historial operativo y de fallos de una máquina. Con este conocimiento, son capaces de construir modelos predictivos que no solo nos alertan sobre una posible falla, sino que ¡estiman el tiempo restante de vida útil (RUL) de un componente con una precisión asombrosa! La IA incluso puede automatizar el diagnóstico y sugerir la solución más adecuada. He visto cómo la IA ha revolucionado por completo la detección de anomalías, pasando de sistemas manuales a soluciones automatizadas que salvan millones.
- Gemelos Digitales (Digital Twins): Un gemelo digital es una réplica virtual y dinámica de un activo físico o de un proceso. Se alimenta con los datos en tiempo real del IIoT y simula el comportamiento del activo real. Un ing en mantenimiento industrial puede usar este gemelo para probar diferentes escenarios ('¿qué pasaría si...?'), para simular reparaciones antes de ejecutarlas en el campo, o para visualizar el impacto de un fallo inminente en el resto del sistema. Todo esto, sin afectar la producción real. Es como tener un laboratorio de pruebas ilimitado.
- Software de Gestión de Mantenimiento Asistido por Ordenador (GMAO/CMMS): Aunque no es una tecnología nueva, el CMMS moderno es el sistema nervioso central que integra todo lo demás. Un Software de Gestión de Mantenimiento avanzado, a menudo basado en la nube, centraliza las órdenes de trabajo, gestiona el inventario de repuestos, planifica las tareas preventivas y, lo más importante, se integra con los sistemas de IIoT y IA para recibir alertas y generar órdenes de trabajo automáticamente. Me permite tener una gestión 360° del ciclo de vida del activo.
- Realidad Aumentada (AR): Imagina esto: un técnico en campo, con unas gafas especiales, ve información digital (esquemas, instrucciones paso a paso, valores de sensores) superpuesta sobre la máquina real. Puede recibir asistencia remota de un ingeniero en mantenimiento experto que está a miles de kilómetros, quien ve exactamente lo que el técnico ve y lo guía en la reparación. Es como tener a un experto contigo en todo momento.
El Nuevo Perfil del Ingeniero en Mantenimiento 4.0: El "Médico" de la Planta Inteligente
Esta revolución tecnológica ha exigido una evolución en nuestro perfil profesional. Los conocimientos tradicionales de la ingeniería mecánica en mantenimiento industrial siguen siendo indispensables, ¡por supuesto! Pero ya no son suficientes. El ingeniero en mantenimiento del futuro, y del presente, debe ser un profesional híbrido con competencias en:
- Ciencia de Datos: La habilidad para entender y analizar datos, interpretar los resultados de los modelos de Machine Learning y tomar decisiones basadas en evidencia estadística. Los números ahora hablan.
- Tecnologías de la Información (IT): Comprensión de redes, ciberseguridad (crucial para proteger nuestros sistemas conectados) y arquitecturas en la nube. Somos cada vez más ingenieros de sistemas.
- Ingeniería de Confiabilidad: Un profundo conocimiento de metodologías como RCM y análisis de causa raíz para aplicar correctamente los insights que la tecnología nos proporciona. La tecnología es una herramienta, no un sustituto de la lógica ingenieril.
- Gestión de Proyectos: La capacidad para liderar proyectos complejos de implementación tecnológica y, no menos importante, gestionar el cambio cultural que conllevan.
- Habilidades Blandas: La comunicación efectiva para justificar inversiones ante la gerencia y para trabajar en equipos multidisciplinarios que incluyen a científicos de datos, expertos en Tecnologías de la Información (IT) y técnicos de campo. Somos un puente entre mundos.
El futuro de la ingeniería en mantenimiento es, sin duda, apasionante y desafiante. Nos estamos moviendo hacia un modelo 'prescriptivo', donde los sistemas no solo predecirán una falla, sino que nos indicarán un conjunto de acciones óptimas para solucionarla, considerando costos, disponibilidad de personal y el plan de producción. En este escenario, el ing en mantenimiento industrial evoluciona de ser un 'mecánico avanzado' a convertirse en un gestor estratégico de activos, un verdadero 'médico' de la planta que utiliza la tecnología más avanzada para diagnosticar, curar y, sobre todo, prevenir enfermedades en el corazón productivo de la empresa. Para profundizar en estas estrategias avanzadas, siempre recomiendo consultar recursos especializados como los que ofrece Reliable Plant, un portal líder en conocimiento sobre confiabilidad y mantenimiento industrial.
La adopción de estas tecnologías ya no es una opción, sino una necesidad imperante para las empresas que desean seguir siendo competitivas. La ingeniería de mantenimiento, armada con el poder de la Industria 4.0, se consolida como una de las funciones más críticas y de mayor valor añadido en el panorama industrial moderno. Y para mí, es un privilegio ser parte de ella.